There are many factors affecting the production efficiency of 1T induction melting furnace. For equipment procurement, we must first pay attention to the efficiency problems caused by the 1T induction melting furnace structure. Induction melting furnace, the structure and size of each part of the furnace body, the materials used in the furnace, the structure of the auxiliary equipment, etc., all belong to the furnace structure.
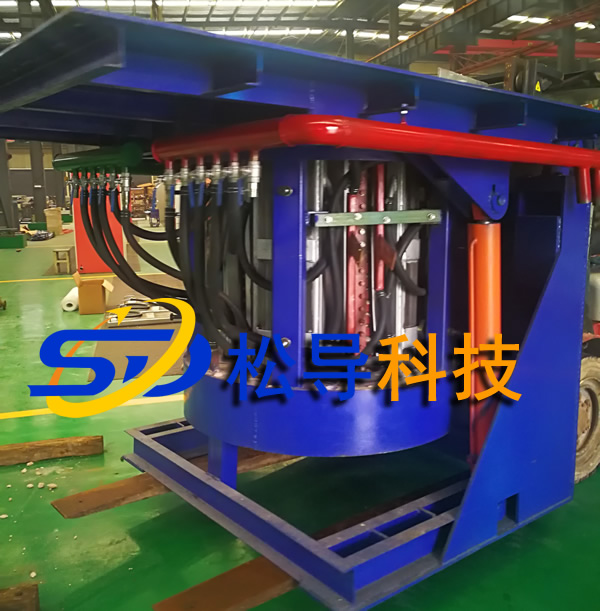
2. Renovation of the old furnace type
Improve the furnace size and size to make it more reasonable. Some furnace types and sizes adopt a universal design, regardless of the specific conditions, such as the size of the billet, and the design has a great difference. These are not conducive to heat exchange, and the furnace type and size should be improved according to practical experience, and the heating of the billet should be accelerated, thereby improving the productivity of the furnace. Reduce the heat loss of the furnace. The heat loss through the furnace and the heat taken away by the cooling water account for 1/4-1/3 of the heat load of the furnace, which not only causes waste of heat energy, but also reduces the temperature of the furnace and affects the heating of the steel. Reducing this loss can increase the output of the furnace. Since the water pipe is in direct contact with the billet, part of the heat taken away by the cooling water is effective heat. Secondly, the black mark is generated in the place where the billet meets the water pipe, which requires a long soaking time to eliminate the black mark, which has an effect on the furnace output. . The use of refractory plastic wrap pipes can increase the furnace productivity by 15%-20%. Recently, the development of a waterless cold rolling heating furnace has also been developed, which also increases the furnace output.
Related products :1T induction melting furnace